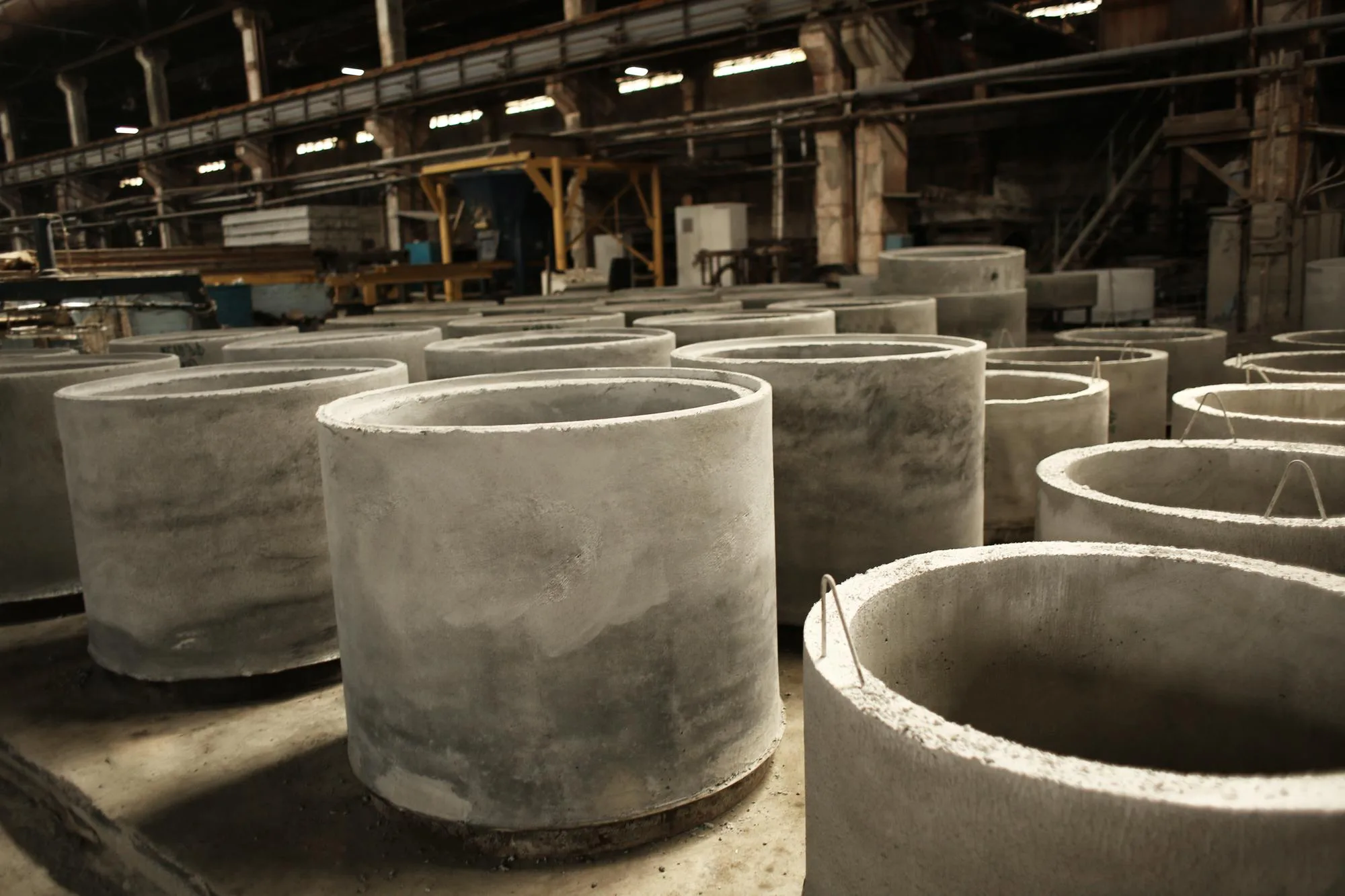
Ceramic manufacturing is an industry that combines ancient art with modern science, producing materials and products that are an integral part of our daily lives. From the mugs we drink our coffee in to the tiles that adorn our homes and the sophisticated components used in electronics and aerospace, ceramics are everywhere. This article explores the world of ceramic manufacturers, shedding light on the processes, innovations, and challenges in this diverse and evolving field.
The Fundamentals of Ceramic Manufacturing
At its core, ceramic manufacturing involves the processing of non-metallic, inorganic materials into solid objects through the application of heat. The process starts with the selection and preparation of raw materials, which often include clay, silica, alumina, and kaolins. These materials are then subjected to various processes such as mixing, shaping, drying, and firing at high temperatures, resulting in the formation of ceramic products with desired properties.
The Wide Array of Ceramic Products
Ceramic manufacturers produce a vast range of products, categorized broadly into traditional ceramics, such as pottery and bricks, and advanced ceramics, such as silicon nitride and zirconia. Traditional ceramics have been around for thousands of years and continue to be in demand for their aesthetic and functional qualities. Advanced ceramics, on the other hand, are known for their exceptional properties, including high temperature resistance, durability, and electrical conductivity, making them essential in industrial, medical, and technological applications.
Innovations and Technologies in Ceramic Manufacturing
The ceramic industry has seen significant advancements in technology and materials science. One of the key innovations is the development of additive manufacturing or 3D printing of ceramics, which allows for the creation of complex shapes and structures that were previously impossible or too costly to produce. This technology has opened up new possibilities in design and functionality, particularly in medical implants, aerospace components, and intricate art pieces.
Digitalization and automation have also transformed traditional manufacturing processes, leading to increased efficiency, precision, and scalability. These advancements help manufacturers meet the growing demand for high-quality ceramic products while reducing waste and energy consumption.
Challenges and Sustainability
Despite the progress, ceramic manufacturers face several challenges. The high energy requirements for firing ceramics can have significant environmental impacts, prompting the industry to explore alternative, more sustainable methods of production. Recycling ceramic waste and developing energy-efficient kilns are among the strategies being implemented to reduce the carbon footprint of ceramic manufacturing.
The global supply chain for raw materials is another area of concern. Fluctuations in availability and prices can affect production costs and lead to market instability. Manufacturers are addressing these challenges by diversifying their supply sources and investing in local materials and technologies.
The Future of Ceramic Manufacturing
The future of ceramic manufacturing lies in innovation, sustainability, and adaptation to changing market needs. As manufacturers continue to explore new materials, processes, and applications, the potential for ceramics expands even further. From enhancing the performance of electronic devices to advancing healthcare solutions and creating more sustainable building materials, the contributions of ceramic manufacturers to society are valuable and far-reaching.