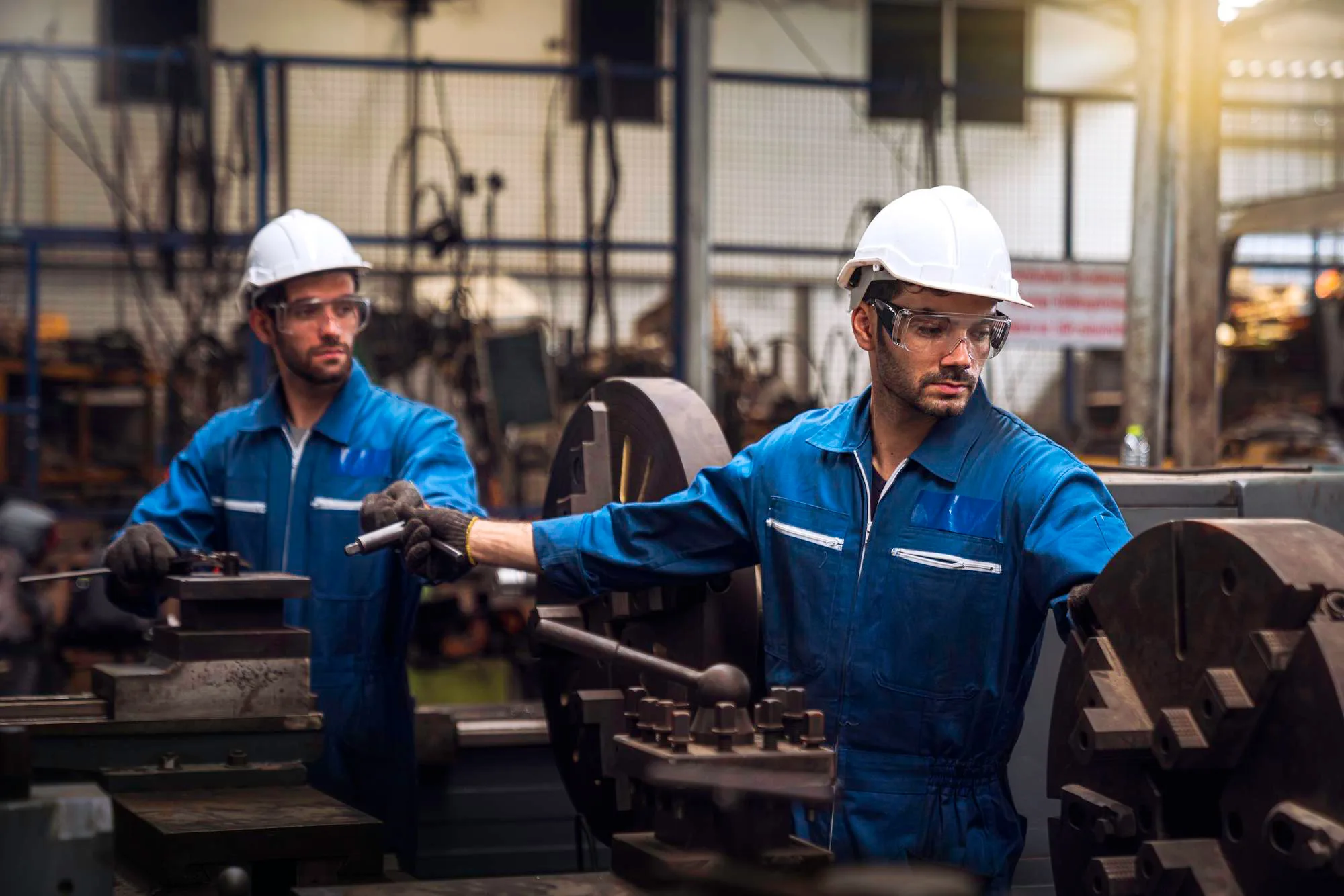
In the vast and dynamic field of industrial processing, agitators play a role in ensuring the efficiency and quality of various manufacturing processes. From chemical production to food and beverages, pharmaceuticals, and more, the choice of the right industrial agitator can significantly impact production outcomes. As such, selecting a reputable manufacturer is essential, and this article can help you understand some key considerations in the process.
What Is an Industrial Agitator?
An industrial agitator is a mechanical device used in various industries to mix liquids, gasses, or slurries and ensure that the mixture is homogeneous in consistency and temperature. This equipment plays a role in processes such as chemical reactions, heat transfer, mass transfer, and phase homogenization.
Industrial agitators can vary significantly in design and function based on the specific needs of the process. Some common types include the following:
- Top-entry agitators: Mounted on the top of the tank, these are suitable for large-scale mixing and can handle a wide range of viscosities.
- Side-entry agitators: Installed on the sides of tanks, these are often used for blending and maintaining homogeneity in large storage tanks.
- Bottom-entry agitators: Positioned at the bottom of a vessel, they are typically used in applications requiring gentle mixing or where headspace is limited.
Chemical, pharmaceutical, food and beverage, cosmetic, and wastewater treatment industries often rely on these agitators for efficient and consistent production processes. The choice of an agitator depends on factors like the type of material to be mixed, the volume of the mixture, viscosity, and the specific process requirements like temperature and pressure.
Key Considerations in Selecting an Agitator Manufacturer
When you’re looking to purchase an agitator, the manufacturer you go with can make a difference in the performance outcomes of the agitator you select. Consider the following when selecting a manufacturer:
- Industry Expertise: Different sectors have unique needs based on the materials processed, the required mixing intensity, and regulatory standards. A manufacturer with specific experience in your industry can better understand these nuances and offer tailored solutions.
- Product Range and Customization: A broad product range is often a sign of a versatile manufacturer. Look for companies that offer a variety of agitators, such as top-entry, side-entry, bottom-entry, and portable models. Customization options are equally important, as they ensure that the agitator matches your process requirements. If you need a highly specialized product, however, opting for a manufacturer that’s more familiar with your industry can be important, even if the company doesn’t offer as many agitator models.
- Quality and Durability: High-quality materials and construction are non-negotiable for equipment that often operates under difficult conditions. Durable agitators reduce downtime and maintenance costs. Check for certifications and compliance with industry-specific standards to gauge quality.
- Technical Support and Service: Reliable after-sales support is critical. A good manufacturer can provide comprehensive installation guidance, troubleshooting, maintenance, and repair services. Accessibility to spare parts and the ability to perform emergency services are also important.
- Innovation and Technology: Leading manufacturers invest in research and development to improve the efficiency and functionality of their agitators. Look for companies that incorporate the latest technologies, such as advanced motor designs, variable speed drives, and smart monitoring systems.
Choosing the right industrial agitator manufacturer involves careful consideration of your specific needs, the manufacturer’s expertise, and the quality of the products and services. By partnering with a reputable provider, you can ensure the reliability and efficiency of your mixing processes, potentially leading to better productivity and profitability in your operations.